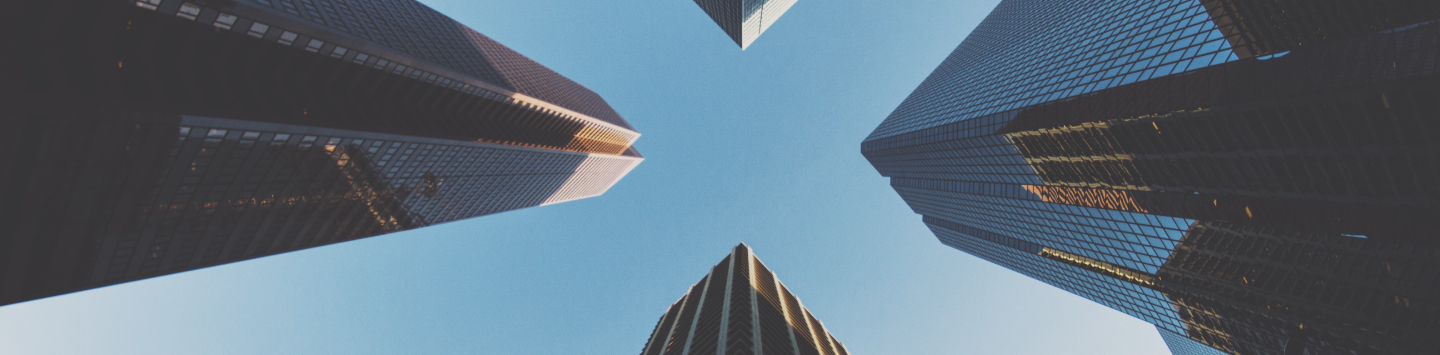
工場DXの進め方
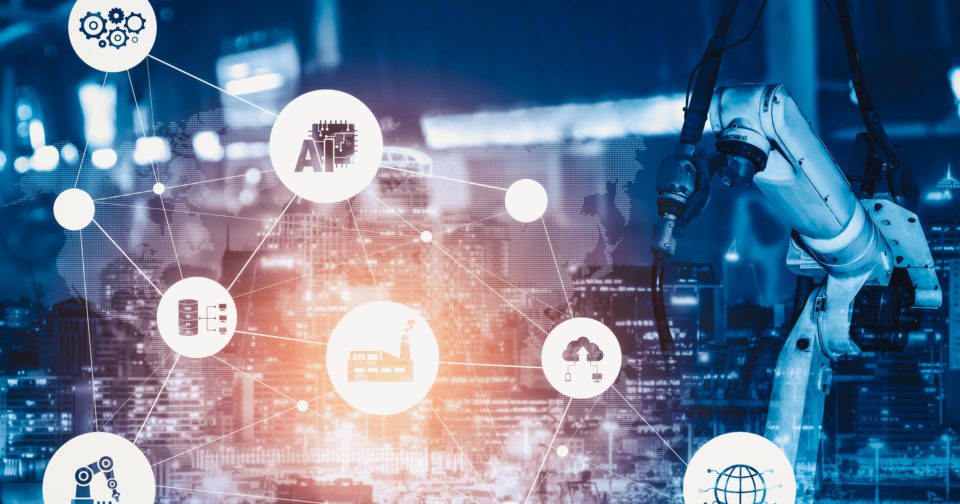
2025年の崖を目前にして、多くの企業がDXの推進を急いでいます。その中で、製造業においては工場DXの重要性が浮き彫りになってきました。そもそもDXは企業全体の変革を目指すものですから、工場だけ別というわけには行かないのですが、工場のDXにはIT系のDXとは異なる課題があり、そこで苦労している企業が多いようです。DXの手法やそれに使われるテクノロジーやソリューションについては、IT系のものがそのまま使える場合も多いのですが、適用方法や運用方法については注意が必要です。今回は工場DXにおいて気をつけるべき点について考えて見ます。
通常のDXについては語り尽くされていますのでここでは触れませんが、工場DXにおいて特に気をつけるべき点として、大きく2つが挙げられます。それは、工場においては部分最適化が想定以上に進んでいる可能性があること、そして特有のセキュリティ環境です。順番に見て行きましょう。
しかし、これまで磨き上げてきたプロセスを見直すというのは想像以上に大変であり、進め方を間違えると大規模な障害を引き起こす可能性もあります。今年に入って、大手企業がDXのためにシステムを刷新したものの、トラブルによりビジネスが停止するといった事例がいくつも起きています。これらのトラブルの原因は現時点では明らかではありませんが、DXの難しさを示す事例として肝に銘じる必要があります。
先に述べたように、現在の現場プロセスは現場の工夫によって究極まで最適化が行われており、そのプロセスに手を加えることには大きなリスクが伴います。長い時間をかけて最適化が進められた現場プロセスには、当初の設計にはなかった機能やモジュールがいつの間にか追加されていたり、独特の手順を導入して問題を切り抜けたりしている場合が多く、それらがドキュメント化されていない場合もあります。通常のシステム更新ではなんとか対応できても、DXという抜本的な改革においては、小さな見落としが大きな問題に発展することがあるのです。
日本には日本のDXがある、という考え方もあります。過去のERPシステムの導入などでも、現場プロセスを一部温存するなど、欧米とは違う独自のアプローチを模索してきました。DXに正解はありませんが、自社にとって何が最適解なのかを探るためにも、現場プロセスの徹底的なレビューが必要です。
幸いに、ITシステムで培ってきたセキュリティテクノロジーの多くがOTでも有効に活用できます。ファイアウォールやIPSのような伝統的なセキュリティデバイスや、SASEやEDRのような最新のゼロトラストソリューションは、そのままOTセキュリティでも有効です。
そして、忘れられがちなのがID管理とアクセス制御です。これまで外部からの脅威に直接さらされずに済んでいたOTシステムでは、古いプラクティスがそのまま残っている場合も少なくありません。管理者パスワードを使い回していたり、複数の担当者が同じ管理者アカウントを共有したりしている場合も多く、複数のアカウントに最高特権が与えられたりしていることもあります。現場での即時かつ柔軟な対応のためにはその方が都合が良かったからでしょうが、これを放置してそのままITシステムや外部と接続すると、あるアカウントのクレデンシャルが漏れた場合に、工場全体、あるいは企業全体が侵害されてしまう危険があります。
最新のプラクティスでは、最小権限の原則に基づいて担当者毎にきめ細かくアクセス権限を付与することで業務に最低限必要な権限以外は与えないようにし、特別にそれが必要な場合は一定の手順に従って期間を限定した権限を付与します。いわゆる、ゼロトラストの考え方です。ひとつの管理者アカウントを複数人で使っていては、何かあったときの原因究明ができませんから、そのようなプラクティスは推奨されません。そして、重要アカウントには多要素認証(MFA)を導入する必要があります。これらの対策はベストプラクティスとしてまとめられていますから、それを参考にしながら適切に適用し、運用することが大切です。
この他にも、製造装置や生産設備などは、そもそも外部との接続が考えられていない場合も多く、通信機能があったとしても、プロトコルが独自だったりセキュリティが弱かったりすることもあります。全体最適のためには、装置や設備などの稼働状況をリアルタイムに収集する必要がありますから、これらの機器をどのようにネットワークに組み込んで行くかも課題となります。その際、装置自体の処理能力が不足する場合もありますから、外付けのファイアウォールやIPSで守り、スイッチやゲートウェイなどで効果的にネットワークをセグメント化して万一の場合にも影響を最少化するなどの対策が有効でしょう。
また、システムの移行に際しては、見落としや不整合が高い確率で起こり得ることを念頭に置いた移行プランを作成することが重要です。「新システムは完璧であるはずだ」といった硬直的な前提の下でプランを作成すると、問題が起きたときに後戻りできません。最近起きたトラブルでも、この点に問題があったのではないかと指摘されている事例もあります。移行は段階的に、何かあったら元に戻れるように。通常でもこういった対策は必要ですが、工場DXの場合には特に気を付けなければならない問題でしょう。
<関連コラム>
今、見直すべきDXの重要性 ~先の見えない時代だからこそ、DXを徹底すべき
DXで具体化する「ソフトウェアの時代」とは
「ゼロトラスト」 ~クラウド時代の新たなセキュリティ~
工場簡易診断サービス
ロボット・自動化導入支援
生産現場向けIoTシステム構築サービス
通常のDXについては語り尽くされていますのでここでは触れませんが、工場DXにおいて特に気をつけるべき点として、大きく2つが挙げられます。それは、工場においては部分最適化が想定以上に進んでいる可能性があること、そして特有のセキュリティ環境です。順番に見て行きましょう。
部分最適化の壁
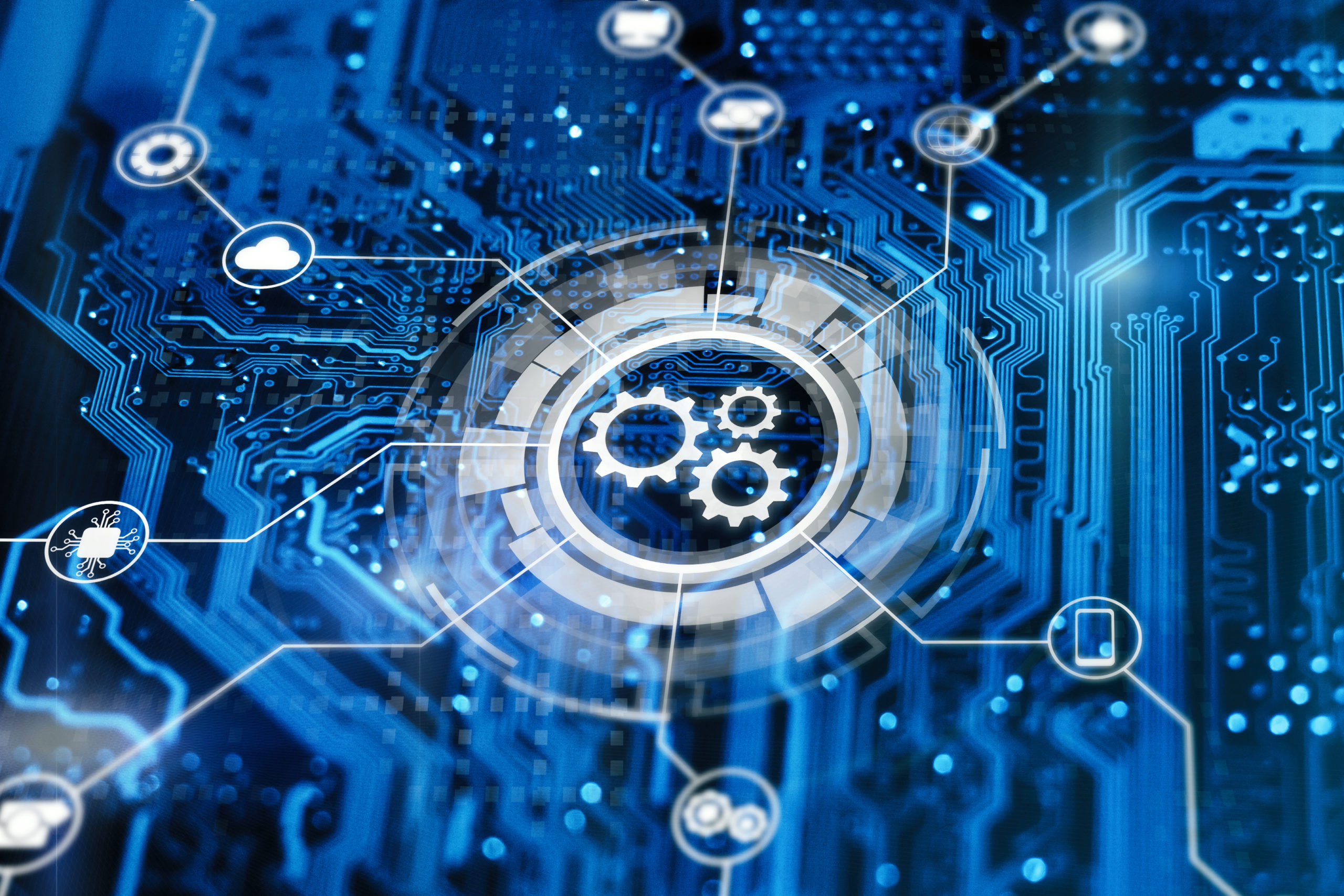
日本の製造業の特徴として、現場の強さが挙げられます。現場での細かい工夫や様々な取り組みがプロセスを改善し、効率化を進め、品質を高めてきました。しかしこれは見方を変えると究極の部分最適であり(もちろん最終的に全体の効率化に貢献していますが)全体を見渡したグランドデザインをベースにしたものでは無い場合も多いようです。これは欧米に対する日本の製造業の特徴でもあり、これまでは日本の強さを支えていました。しかし、DXの本質は全社的なビジネスプロセスの改革であり、全体最適を目指して各部をそれに合わせていくということです。
しかし、これまで磨き上げてきたプロセスを見直すというのは想像以上に大変であり、進め方を間違えると大規模な障害を引き起こす可能性もあります。今年に入って、大手企業がDXのためにシステムを刷新したものの、トラブルによりビジネスが停止するといった事例がいくつも起きています。これらのトラブルの原因は現時点では明らかではありませんが、DXの難しさを示す事例として肝に銘じる必要があります。
先に述べたように、現在の現場プロセスは現場の工夫によって究極まで最適化が行われており、そのプロセスに手を加えることには大きなリスクが伴います。長い時間をかけて最適化が進められた現場プロセスには、当初の設計にはなかった機能やモジュールがいつの間にか追加されていたり、独特の手順を導入して問題を切り抜けたりしている場合が多く、それらがドキュメント化されていない場合もあります。通常のシステム更新ではなんとか対応できても、DXという抜本的な改革においては、小さな見落としが大きな問題に発展することがあるのです。
日本には日本のDXがある、という考え方もあります。過去のERPシステムの導入などでも、現場プロセスを一部温存するなど、欧米とは違う独自のアプローチを模索してきました。DXに正解はありませんが、自社にとって何が最適解なのかを探るためにも、現場プロセスの徹底的なレビューが必要です。
OTセキュリティ
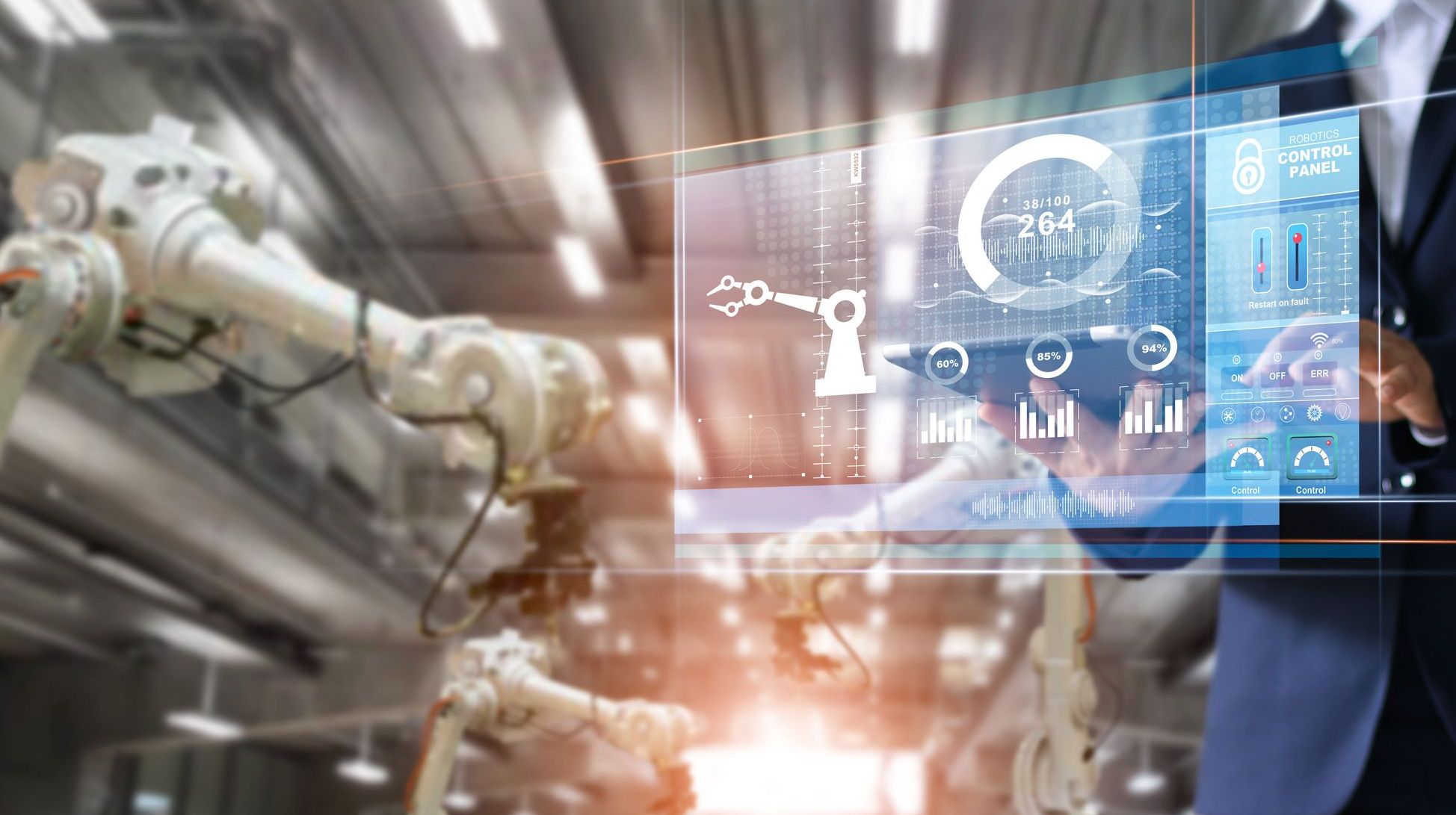
工場や社会インフラを制御・運用するためのOT(Operational Technology)は、セキュリティ面での懸念や安定稼働への要求から、ITシステムやクラウドのような外部システムとの接続をなるべく行わないという考え方で構築・運用されてきました。そもそも接続するメリットが少ないと考えられたことも原因でしょう。しかし今後DXを進めるにあたっては、外部との接続は避けられません。DXとは全社最適化であり、ITとOTを統合して本社、支店、工場などを統合管理することで効率を究極まで高めようとするものだからです。さらに、生成AIのような負荷の大きな処理については外部のサービスを使わざるを得ませんし、セキュリティパッチの適用やポリシーのアップデートなどもオンライン化して自動化する必要があります。このほかにも、最新の技術をタイムリーに取り込んで効率化を進めるためには、OTとITの連携が必要不可欠です。OTシステムの抜本的な見直しは、避けて通れない道なのです。
幸いに、ITシステムで培ってきたセキュリティテクノロジーの多くがOTでも有効に活用できます。ファイアウォールやIPSのような伝統的なセキュリティデバイスや、SASEやEDRのような最新のゼロトラストソリューションは、そのままOTセキュリティでも有効です。
そして、忘れられがちなのがID管理とアクセス制御です。これまで外部からの脅威に直接さらされずに済んでいたOTシステムでは、古いプラクティスがそのまま残っている場合も少なくありません。管理者パスワードを使い回していたり、複数の担当者が同じ管理者アカウントを共有したりしている場合も多く、複数のアカウントに最高特権が与えられたりしていることもあります。現場での即時かつ柔軟な対応のためにはその方が都合が良かったからでしょうが、これを放置してそのままITシステムや外部と接続すると、あるアカウントのクレデンシャルが漏れた場合に、工場全体、あるいは企業全体が侵害されてしまう危険があります。
最新のプラクティスでは、最小権限の原則に基づいて担当者毎にきめ細かくアクセス権限を付与することで業務に最低限必要な権限以外は与えないようにし、特別にそれが必要な場合は一定の手順に従って期間を限定した権限を付与します。いわゆる、ゼロトラストの考え方です。ひとつの管理者アカウントを複数人で使っていては、何かあったときの原因究明ができませんから、そのようなプラクティスは推奨されません。そして、重要アカウントには多要素認証(MFA)を導入する必要があります。これらの対策はベストプラクティスとしてまとめられていますから、それを参考にしながら適切に適用し、運用することが大切です。
この他にも、製造装置や生産設備などは、そもそも外部との接続が考えられていない場合も多く、通信機能があったとしても、プロトコルが独自だったりセキュリティが弱かったりすることもあります。全体最適のためには、装置や設備などの稼働状況をリアルタイムに収集する必要がありますから、これらの機器をどのようにネットワークに組み込んで行くかも課題となります。その際、装置自体の処理能力が不足する場合もありますから、外付けのファイアウォールやIPSで守り、スイッチやゲートウェイなどで効果的にネットワークをセグメント化して万一の場合にも影響を最少化するなどの対策が有効でしょう。
「見えない障害」に備えた移行プランが必要
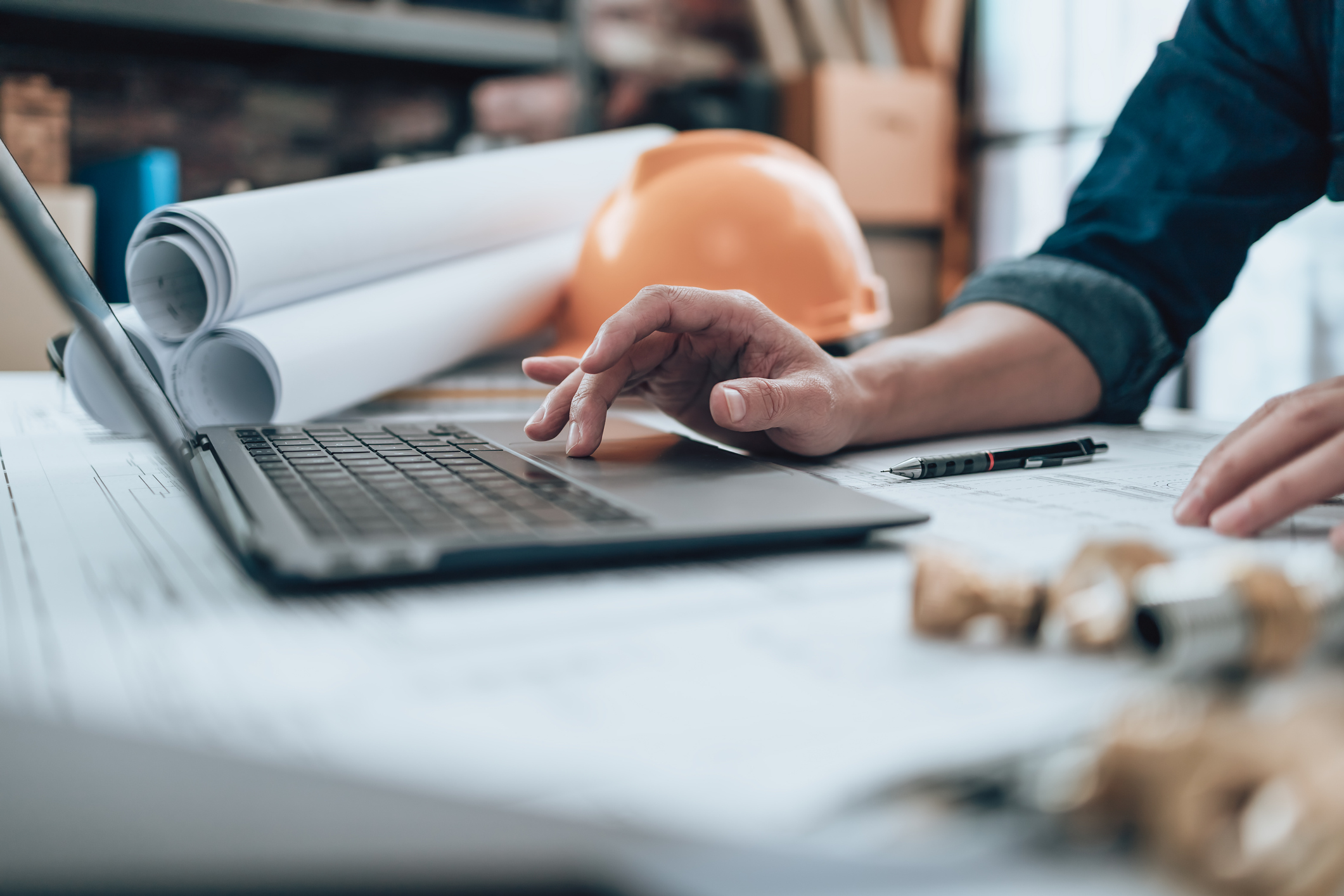
このような対策は、これまでの現場での運用に大きな影響を及ぼす可能性があり、現場からの抵抗が大きくなることも予想されます。リスクをとって将来へ向けての効率化をとるか、安定稼働を優先するかは難しい経営判断になりますが、本来のDXの目的を考えれば、こうした「現場合わせ」を洗い出し、正規のプロセスとしてドキュメント化していく必要があります。
また、システムの移行に際しては、見落としや不整合が高い確率で起こり得ることを念頭に置いた移行プランを作成することが重要です。「新システムは完璧であるはずだ」といった硬直的な前提の下でプランを作成すると、問題が起きたときに後戻りできません。最近起きたトラブルでも、この点に問題があったのではないかと指摘されている事例もあります。移行は段階的に、何かあったら元に戻れるように。通常でもこういった対策は必要ですが、工場DXの場合には特に気を付けなければならない問題でしょう。
<関連コラム>
今、見直すべきDXの重要性 ~先の見えない時代だからこそ、DXを徹底すべき
DXで具体化する「ソフトウェアの時代」とは
「ゼロトラスト」 ~クラウド時代の新たなセキュリティ~
ミツイワが提供する工場DXソリューション
スマートファクトリー支援工場簡易診断サービス
ロボット・自動化導入支援
生産現場向けIoTシステム構築サービス